Boiler Feed Pump Calculator
How to Use the Boiler Feed Pump Calculator Effectively
Maximize the accuracy and usefulness of the Boiler Feed Pump Calculator by carefully entering the following values. Here are detailed instructions along with example inputs different from the default placeholders:
- Feedwater Temperature (°C): Enter the temperature of the feedwater entering the pump. For example: 95°C for moderate-temperature boiler systems, or 160°C for superheated steam applications.
- Boiler Operating Pressure (bar): Specify the pressure inside the boiler where the feedwater is delivered. Example values: 45 bar for medium-pressure boilers, or 110 bar for high-pressure power plant boilers.
- Feedwater Flow Rate (m³/h): Provide the volume flow rate of feedwater needed by the boiler. Example inputs: 35 m³/h for small process boilers, or 600 m³/h for industrial-scale operations.
- Suction Pressure (bar): Enter the absolute pressure at the pump’s suction side. Examples: 1.8 bar typical for deaerator outlets, or 0.9 bar for systems with slight vacuum conditions.
- Suction and Discharge Elevations (m): Input the elevation heights relative to the pump centerline. For example: suction elevation of 4.5 m and discharge elevation of 12 m.
- Suction and Discharge Pipe Dimensions: Specify internal diameters in millimeters and lengths in meters. Sample values: suction pipe diameter 180 mm with 20 m length; discharge pipe diameter 130 mm with 65 m length.
- Pipe Material: Select from steel, PVC, or copper to factor in pipe roughness impacting friction loss calculations.
- Pump Efficiency (%): Enter the efficiency at which your pump operates. If unknown, the default value of 75% is used. Example input: 82% for a well-maintained, modern pump.
- NPSH Required (m): Input the Net Positive Suction Head as per your pump’s datasheet to ensure cavitation prevention. Examples: 7 m for a standard vertical pump, or 10 m for high-speed pumps.
- Calculate: After all inputs are filled, click “Calculate” to receive your pump’s performance metrics including total head, pump power, available NPSH, and friction losses.
This step-by-step input process guarantees precise, reliable results tailored to your boiler feed pump system.
Introduction to the Boiler Feed Pump Calculator: Definition, Purpose, and Benefits
The Boiler Feed Pump Calculator is a specialized tool designed to simplify complex hydraulic analyses related to boiler feed pumps used in steam generation systems. It aids engineers, plant operators, and maintenance teams by providing quick, accurate calculations for pump performance parameters—enabling optimized operation and system reliability.
What is the Boiler Feed Pump Calculator?
This calculator evaluates essential metrics such as total pump head, power requirements, Net Positive Suction Head (NPSH), and pipeline friction losses based on user inputs including water temperature, system pressure, flow rate, pipe characteristics, and pump efficiency.
Purpose and Core Benefits
- Optimize pump selection: Ensure right-sized pumps to meet system demands without oversizing or undersizing.
- Improve operational efficiency: Minimize energy consumption through accurate power calculation tailored to operating conditions.
- Prevent cavitation damage: Compare available NPSH with required NPSH to avoid cavitation risk and extend pump life.
- Streamline system design: Quickly assess piping friction impact and elevation changes affecting pump head.
- Save time and resources: Replace manual calculations with fast, error-free automated results.
Why Accurate Boiler Feed Pump Calculations Matter
Accurate pump calculations are vital for maintaining smooth boiler operation, safeguarding against unexpected downtime, and ensuring compliance with safety standards. Reliable data helps avoid costly repairs and optimize system longevity while maintaining stable steam production—a critical factor in industrial and power generation sectors.
Example Calculation Using the Boiler Feed Pump Calculator
Consider a boiler feed pump system with the following inputs:
- Feedwater temperature: 100°C
- Boiler operating pressure: 70 bar
- Flow rate: 120 m³/h
- Suction pressure: 2.2 bar
- Suction elevation: 5 m
- Discharge elevation: 15 m
- Suction pipe diameter: 160 mm, length: 25 m
- Discharge pipe diameter: 120 mm, length: 70 m
- Pipe material: Steel
- Pump efficiency: 78%
- NPSH Required: 6 m
Calculation Details
The calculator computes the total pump head combining pressure, elevation, and friction losses with the formula:
$$ \text{Total Pump Head} = H_p + H_s + H_f + H_e $$- Pressure head, (H_p): Generated from boiler and suction pressures.
- Static head, (H_s): Difference in elevation between suction and discharge points.
- Friction head, (H_f): Pressure losses due to pipe friction on suction and discharge sides.
- Elevation head, (H_e): Net height difference affecting pumping power.
For this example, expected outputs might include:
- Total Pump Head: Approximately 880 meters
- Power Required: Around 240 kW (adjusted for 78% pump efficiency)
- NPSH Available: 9.3 meters
- NPSH Verification: Acceptable (since available NPSH exceeds required 6 meters)
- Friction Losses: Detailed values for suction and discharge pipe friction head losses
Benefits of This Calculation
- Enables precise pump sizing to enhance system efficiency.
- Helps prevent damaging cavitation by verifying NPSH margins.
- Assists in optimizing piping design to reduce unnecessary pressure losses.
- Guides operational adjustments such as flow rate reduction or pipe replacement.
Is this tool helpful?
Important Disclaimer
The calculations, results, and content provided by our tools are not guaranteed to be accurate, complete, or reliable. Users are responsible for verifying and interpreting the results. Our content and tools may contain errors, biases, or inconsistencies. We reserve the right to save inputs and outputs from our tools for the purposes of error debugging, bias identification, and performance improvement. External companies providing AI models used in our tools may also save and process data in accordance with their own policies. By using our tools, you consent to this data collection and processing. We reserve the right to limit the usage of our tools based on current usability factors. By using our tools, you acknowledge that you have read, understood, and agreed to this disclaimer. You accept the inherent risks and limitations associated with the use of our tools and services.
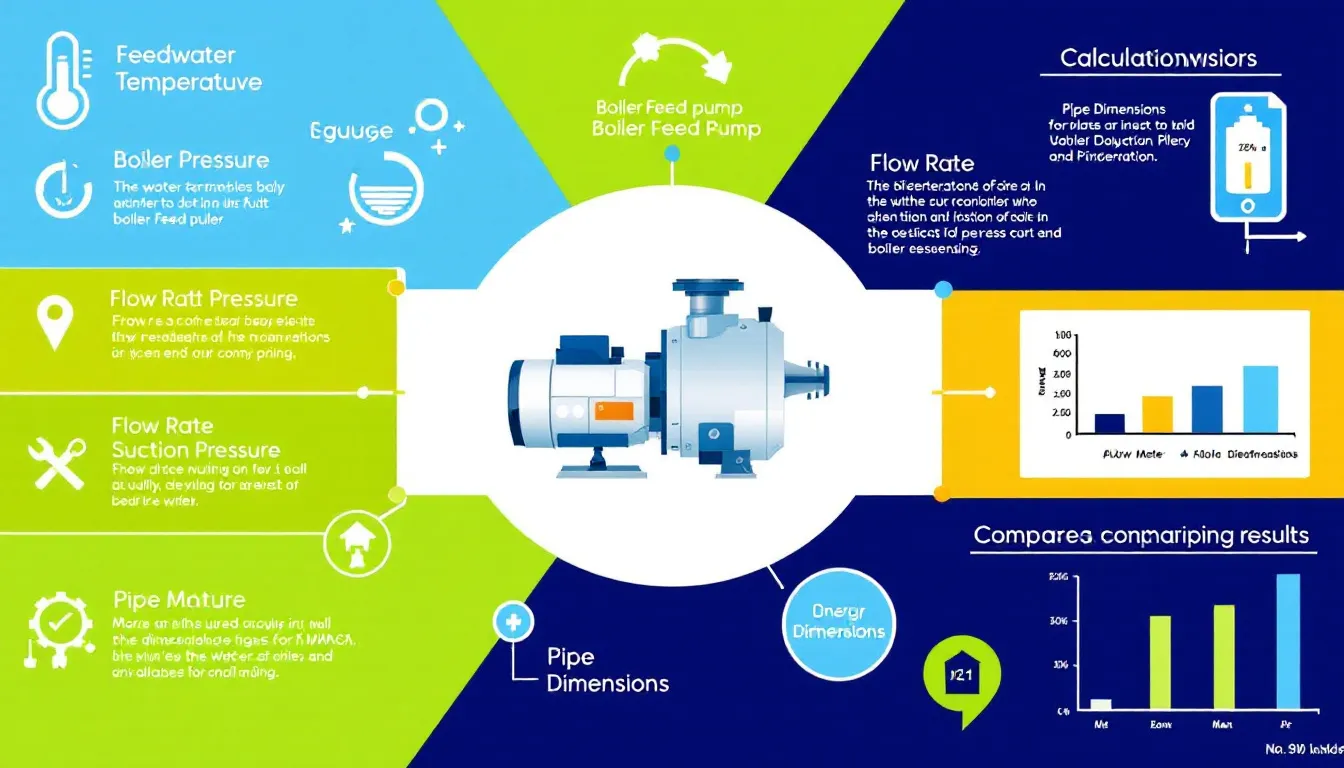