Boiler Feed Pump Calculator
Is this tool helpful?
How to Use the Boiler Feed Pump Calculator Effectively
Use this boiler feed pump calculator to quickly determine essential performance parameters for your pumping system. Follow these steps to get accurate results:
- Flow Rate (m³/h): Enter the desired water flow through the pump. For example, try 60 m³/h for a small industrial boiler or 130 m³/h for a large-scale operation.
- Fluid Density (kg/m³): Input the density of the fluid at its operating temperature. For instance, use 980 kg/m³ for water at 70°C or 995 kg/m³ for water around 30°C.
- Pump Efficiency: Specify the pump’s efficiency as a decimal between 0 and 1. Typical values range from 0.70 to 0.82.
- Static Head (m): Input the vertical height difference between the pump’s suction and discharge points. Common values might include 18 m or 25 m depending on your system setup.
- Pipe Length (m): Enter the total length of your piping, including fittings and bends. Examples could be 40 m for a compact system or 80 m for larger piping networks.
- Pipe Diameter (m): Provide the internal diameter of the pipe. Use values like 0.08 m for smaller pipes or 0.15 m for larger diameter systems.
- Suction Pressure (Pa): Add the pressure measured on the suction side of the pump. This might be around 90,000 Pa for low-pressure systems or 110,000 Pa for higher-pressure setups.
- Discharge Pressure (Pa): Input the pressure at the pump discharge, such as 280,000 Pa or 350,000 Pa for various boiler operating conditions.
Introduction to the Boiler Feed Pump Calculator: Purpose and Benefits
The boiler feed pump calculator is designed to help you size and analyze boiler feed pump systems efficiently. It calculates key parameters like Total Dynamic Head (TDH), required pump power, flow velocity, and friction head loss based on your specific system inputs.
Using this tool aids in:
- Accurate pump sizing for different boiler systems
- Optimizing energy consumption with precise power requirements
- Preventing cavitation by analyzing pressure and head losses
- Saving time with easy hydraulic calculations for pump selection
- Improving reliability through proper system design and evaluation
Example Calculation Using the Boiler Feed Pump Calculator
To demonstrate how this JavaScript-based tool works, consider a boiler feed system with these parameters:
- Flow Rate: 90 m³/h
- Fluid Density: 975 kg/m³ (water at approximately 85°C)
- Pump Efficiency: 0.80
- Static Head: 20 meters
- Pipe Length: 70 meters
- Pipe Diameter: 0.12 meters
- Suction Pressure: 105,000 Pa
- Discharge Pressure: 340,000 Pa
Calculated System Parameters
- Total Dynamic Head (TDH): About 49.3 meters
- Required Pump Power: Approximately 16.9 kW
- Flow Velocity: Around 2.5 m/s
- Friction Head Loss: Approximately 7.6 meters
Mathematical Formulas Used
The Total Dynamic Head (TDH) combines static lift, friction losses, and pressure differences as:
$$ TDH = H_{static} + H_{friction} + \frac{P_{discharge} – P_{suction}}{\rho g} $$Calculate the required pump power with the formula:
$$ P = \frac{Q \times \rho \times g \times TDH}{\eta \times 1000} $$Where:
- Q = flow rate in cubic meters per second (m³/s)
- ρ = fluid density (kg/m³)
- g = acceleration due to gravity (9.81 m/s²)
- TDH = total dynamic head (meters)
- η = pump efficiency (decimal between 0 and 1)
Applications of the Boiler Feed Pump Calculator in Industry
Power Generation
Accurately sizing boiler feed pumps helps run power plants efficiently across capacities:
- Small-scale plants (20 to 50 MW)
- Medium facilities (100 to 300 MW)
- Large power stations exceeding 500 MW
Process Industry Uses
This calculator aids pump selection for various processing industries:
- Chemical manufacturing plants
- Petrochemical refineries
- Food and beverage production
- Textile and fabric processing
Frequently Asked Questions About Boiler Feed Pump Calculations
Why Calculate Total Dynamic Head?
Calculating TDH gives you the total height and pressure your pump must overcome for reliable, efficient operation.
How Does Pump Efficiency Affect Energy Use?
Higher efficiency lowers power consumption, cutting operating costs. Pumps with 80% efficiency use less energy than those at 70% while delivering the same flow and head.
Why Is Flow Velocity Important?
Maintaining appropriate flow velocity reduces pipe erosion and friction losses. Ideal speeds range from 1.5 m/s to 3.0 m/s for boiler feed systems.
How Often Should You Recalculate Pump Parameters?
Review calculations when system modifications occur—like changes in piping, pressure, or fluid temperature—to ensure continued efficiency.
What Role Does Fluid Density Play?
Fluid density directly impacts both power needs and pressure heads. Accuracy matters especially since density changes with temperature.
Optimization Tips for Your Boiler Feed Pump System
- Track pump efficiency regularly and update calculations as needed
- Adjust for seasonal temperature effects on fluid properties
- Account for pipe scaling or corrosion when estimating friction factors
- Keep detailed records of system changes and recalculations
- Use this calculator for both new projects and system upgrades to maintain optimal performance
Important Disclaimer
The calculations, results, and content provided by our tools are not guaranteed to be accurate, complete, or reliable. Users are responsible for verifying and interpreting the results. Our content and tools may contain errors, biases, or inconsistencies. We reserve the right to save inputs and outputs from our tools for the purposes of error debugging, bias identification, and performance improvement. External companies providing AI models used in our tools may also save and process data in accordance with their own policies. By using our tools, you consent to this data collection and processing. We reserve the right to limit the usage of our tools based on current usability factors. By using our tools, you acknowledge that you have read, understood, and agreed to this disclaimer. You accept the inherent risks and limitations associated with the use of our tools and services.
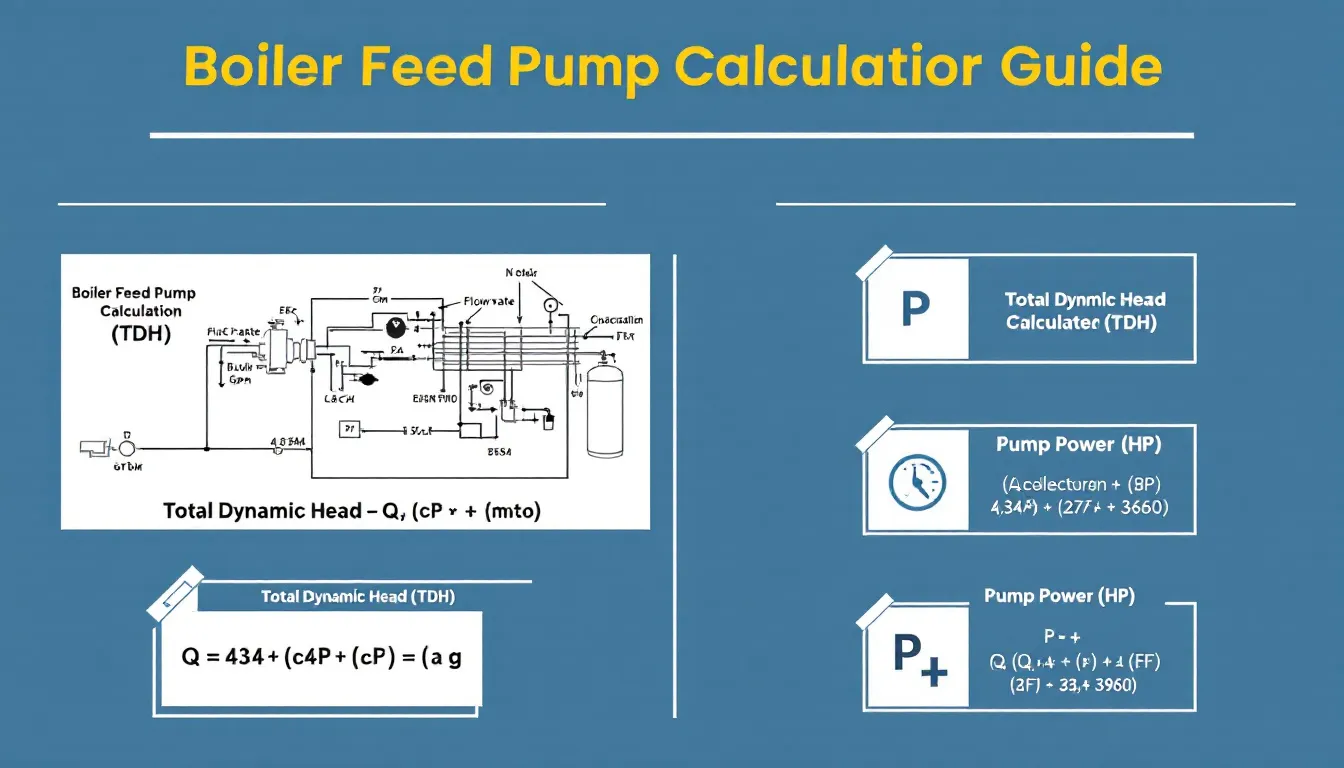