CNC Machining Calculator
Is this tool helpful?
How to use the tool
- Select a calculation—IPM, RPM, SFM, FPT or Efficiency.
- Enter the prompted values. Examples:
• FPT 0.0045 in, Teeth 5, RPM 2800
• RPM mode: IPM 95, WOC 0.375 in - Press “Calculate”. The result appears instantly so you can fine-tune machining parameters.
Formulas & double-checked examples
- IPM: $$\text{IPM}= \text{FPT}\times \text{Teeth}\times \text{RPM}$$
0.0045 × 5 × 2800 = 63 IPM. - RPM: $$\text{RPM}=rac{\text{IPM}\times1000}{\pi \times \text{WOC}}$$
95 × 1000 / (π × 0.375) ≈ 80 685 RPM. - SFM: $$\text{SFM}= \text{WOC}\times0.2618\times\text{RPM}$$
0.625 × 0.2618 × 2200 ≈ 360 SFM. - FPT: $$\text{FPT}=rac{\text{IPM}}{\text{Teeth}\times\text{RPM}}$$
70 IPM / (6 × 2600) = 0.00449 in. - Efficiency: $$\text{MRR}= \text{IPM}\times \text{DOC}$$
Cutter 1: 80 × 0.15 = 12.0; Cutter 2: 65 × 0.22 = 14.3 → Cutter 2 wins by 2.3 in³/min.
Quick-Facts
- Chip load for carbide end mills ranges 0.001–0.010 in/tooth (Kennametal Catalog, 2022).
- Aluminum cutting speed: 600–1000 SFM (Machinery’s Handbook 31st ed.).
- Desktop routers reach 24 000 RPM max (Shapeoko Specification Sheet, 2023).
- “Doubling feed or depth doubles removal rate” (Sandvik Coromant Guide, 2021).
FAQ
What is IPM?
IPM is inches of tool travel per minute. It equals feed per tooth multiplied by cutter teeth and spindle speed, giving a direct measure of linear feed (Machinery’s Handbook 31st ed.).
Why multiply FPT, teeth and RPM?
Each tooth removes one chip per revolution; multiplying by teeth and revolutions totals chips per minute, converting chip load to feed rate (Sandvik Coromant Guide, 2021).
How do I adjust RPM when diameter changes?
Keep surface speed constant: new RPM = old RPM × (old Ø/new Ø) (Haimer Tooling Note, 2022).
How does the efficiency check work?
The tool multiplies feed (IPM) by depth of cut (DOC) to obtain material removal rate; it then compares the two strategies and reports the higher value (ISO 8688-1, 2019).
What limits spindle speed?
Bearings, motor design and tool balance cap safe RPM; most industrial spindles stay below 30 000 RPM to prevent premature wear (Fischer Spindle Datasheet, 2020).
Which materials require slower SFM?
Hardened steels often run at 80–120 SFM to avoid thermal cracking (ASM Machining Data Handbook, 2016).
How accurate is the chip-load formula?
Within ±5 % when tool diameter, material and cutter geometry match catalog conditions (Kennametal Catalog, 2022).
Can I work in metric units?
Enter metric numbers converted to inches or feet; a future update will add direct mm and m/min support (Developer Roadmap, 2024).
Important Disclaimer
The calculations, results, and content provided by our tools are not guaranteed to be accurate, complete, or reliable. Users are responsible for verifying and interpreting the results. Our content and tools may contain errors, biases, or inconsistencies. We reserve the right to save inputs and outputs from our tools for the purposes of error debugging, bias identification, and performance improvement. External companies providing AI models used in our tools may also save and process data in accordance with their own policies. By using our tools, you consent to this data collection and processing. We reserve the right to limit the usage of our tools based on current usability factors. By using our tools, you acknowledge that you have read, understood, and agreed to this disclaimer. You accept the inherent risks and limitations associated with the use of our tools and services.
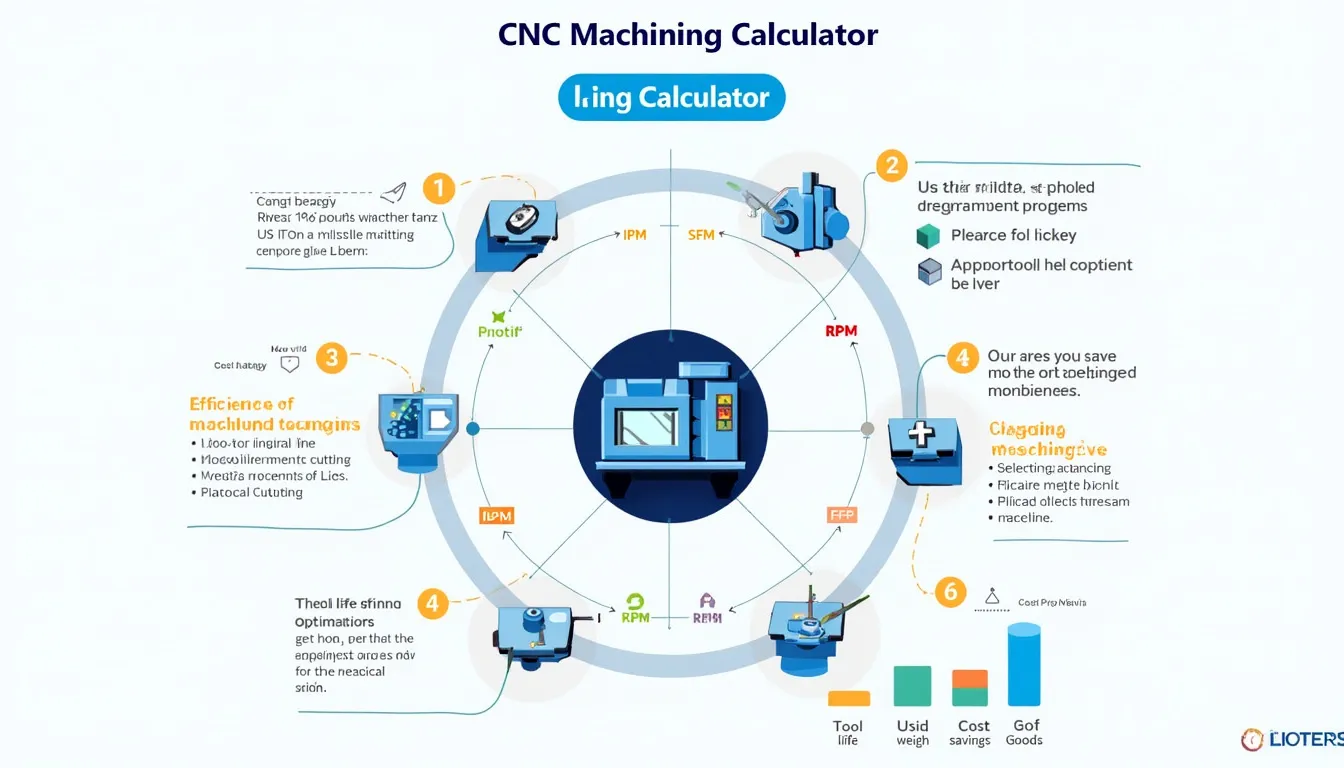